Introduction: How to Make a Beautiful Lizard From Simple Scrap Metal
I made a really cool looking lizard using scrap metal I had laying around the garage, and you can too. One of the best things is that you can make many substitutions to this and it will still look great! *look for the *asterisk* in some of the steps for alternative suggestions*.
It's relatively easy. It just requires a few tools, some patience, time, and the desire to learn.
Here, let me show you how I did it....
Supplies
Here is a comprehensive list of materials based on the 4 main sections of this project
- (A): Hands/Legs
- (B): Body
- (C): Tail
- (D): Heat Treating
Don't get discouraged if you don't have every item listed. As mentioned, there are a lot of options to substitute, and many items are optional if you don't have them.
Proper safety gear is implied for the entire project, even if not specifically mentioned for each step. Use your own discretion
Heat resistant gloves, protective eyewear/face shield are recommended
Hands/Legs Material Prep:
-Electric drill or drill press (corded preferred)
-(4x) 5/16" x 4" hex bolts ***Length and size depends on the size of the lizard you want to make. Thread and head type does not matter.
-Felt tipped marker (to mark the bolts)
-Dremel with cut-off wheels (or hacksaw, or angle grinder with cut off wheel)
-Metal files (having both rounded and flat are ideal)
-Sandpaper or emery cloth
-Propane/Mapp gas torch
-Hammer
-Pliers
Body Material Prep:
-Image of lizard for reference
-1.5" x 0.5" x 8" flat bar. ***This can easily be substituted. Thick flat bar is best. Length and width are proportionate to the desired size lizard you want to make**
-Angle grinder (with at least 1 cut-off wheel and 1 flap disc. ***Grinding disc and polishing pad are optional)
-Felt tipped marker
-Spray paint ***This is completely optional, and only used to outline your reference image to your material. Pen, marker or any kind of paint would be sufficient***
-Metal files
-Sandpaper or emery cloth
-Drill and 3/16'" drill bit ***Size of bit can be substituted. This is for the eyes, and attaching the arms/legs to the body
-6mm flat-backed gems ***Can be substituted for anything else you would rather use for eyes
-Superglue
Attaching Arms/Legs to body
TIG welder *Completely optional* (If you don't weld, solder is fine)
Solder and flux
Tail & Heat Treating Material Prep:
-Propane/Mapp torch
-pliers
-Alcohol or acetone
-Rubber gloves
Step 1: Creating the Arms and Legs
Before proceeding, I recommend viewing the attached video for this step. It is a brief overview of this entire step, and may help to see the process visually ahead of time.. (I recorded this video the last time I made this project, so the angles of the video and still photos may look slightly different).
Using an image for reference is a huge benefit. In this project, maintaining your proportions is what's going to give it a more realistic feel and a reference image definitely helps with that. You can find a great reference picture online with a simple Google search. Pick the top view profile of a lizard that you like the best. I recommend printing out a few copies, as you will need these to refer to throughout the build, and in different capacities.
I like to do this step first because the arms and legs need to be in proportion to the body, and this step often has a little variance between design and execution. Don't be discouraged if it doesn't come out exactly as originally planned, it's not a big deal. You're going to use your electric drill as a mini metal lathe for this project. This is why I recommend a corded drill, so you don't have to worry about battery life getting in the way. If you don't have one right now, you likely can find a used one for cheap on facebook marketplace, craigslist etc. I ended up buying a drill I found new on Amazon for about $25.
Do your best to pick bolts for the legs that can offer the thickness you need when you file the thread down.
Also be sure that the bolts you select are longer than you need by at least 1" so that the drill chuck has something to hold on to. Coarse thread is more difficult to use than fine threaded bolts simply because the file wants to walk down the shaft when spinning in the drill. 18 tpi or more is best....Let me explain further....
You are going to do this step 4 times (2 arms, 2 legs)
- Mark your bolts in 4 sections as shown. 1 section will be the hands/feet, one for the lower arm/leg, one for the upper arm/leg, and the last part will be where you insert into the body when you assemble. (more on that later)
- Secure the drill into a vice or any place you can safely clamp to a table. It has to be very sturdy.
- Cut the head of the bolt off and insert the bolt into the drill with the sections you drew at the other end as pictured.
- Turn the drill on.
- With a rounded file, gently but firmly place the file on the lines that you drew. A round file works best initially because it doesn't get caught in the threads, and its easier to keep your sections correct. Continue to file the bolt into the shape shown using a combination of files until all of the thread is removed in the sections you created. Its ok to leave thread at the very end of the bolt as this will be the hand/foot and we want that as thick as possible (more about that later) Everyone has their own technique, so use what works best for you.
Step 2: Creating the Arms & Legs Continued- Shaping & Positioning
- Now that we have our arms and legs made, it's time to shape the hands and feet. This is done by heating the tip of the metal until its red hot and pounding it flat with a hammer, attempting to widen it as much as possible without getting too thin. You want to fan the metal out as it goes to the tip, creating a cone-like shape. Be careful to only strike the section at the very end as you don't want to ruin the nice shaping you just spent doing on the rest of the arm/leg.
- After you have flattened the tips, draw 3 lines vertically on them. These are your cut lines separating the fingers/toes from each other. (I found that even though 5 digits are anatomically correct, they are too thin. 4 seems best, but that's up to you to decide. Place the bolt in the vice and use a hacksaw or Dremel or grinder with cut-off wheel to cut where you marked your lines.
- Once the cutting is complete, Its now time to shape them. Up until now, all 4 bolts will look identical for the most part. Use your image for reference as to which one is going to be each limb. Using a torch to heat until red hot, very carefully bend them into the desired position. If you attempt to bend them prior to getting red hot, they will very likely snap off. I know this from prior experience and if you've made it to this point, you know how much time would be wasted by it breaking so take your time and heat it thoroughly.
- Once you have each limb positioned to your liking (there will be opportunities to make minor adjustments later) its time to sand and smooth them. Use sandpaper or an emery cloth (600 grit is great, but use what you have) to smooth as much as you can. Cutting the emery cloth or sandpaper into small strips, makes for easy sanding in the hard to reach places between the fingers etc.
- At that point, cut off the remaining threaded portion. Set the arms and legs aside. It's now time to make the body.
Step 3: Creating the Body
Take a copy of your reference image and modify it, if need be to your liking. You can see in the images that I wanted more of a gecko style lizard, which required a thicker body and head so I just drew it in myself.
- Cut the image out with an X-Acto blade or scissors. Don't include the legs, but know exactly how they're positioned on the body. This can be accomplished by leaving a tiny bit of the leg/arm in the cut out, but will eventually be filed down and removed. The tail can just be a straight line of thick material for now, You'll shape it in the next step. Be as accurate as you can when cutting out the torso and head.
- Put the paper image you just cut out on metal flat bar. Spraying with a little spray adhesive helps keep it in place. Or you can tape it, glue it etc
- The paper image is now acting as a stencil. Spray the flat bar and stencil completely with spray paint. It does not matter what color, and does not matter what type of paint. ** you can use pen if you don't have any paint. Once complete, remove the stencil. This has created a silhouette of the exact size torso, and head that you're going to be working towards.
- Place the flat bar in a vice and begin cutting out around your image. This is just for the sides of the image. Not the top and not the bottom. Anywhere that has paint, cut it out by using a grinder with cut-off wheel as best as you can. It does not need to be perfect, but don't go inside the lines. Stay to the outside of the image. Once you've removed all you can with a cut off wheel it's time to use a grinder wheel. Remove as much as you can. Then switch to a flap disc to smooth out the sides. Don't do anything with the tail yet. Cut it into a relatively thick straight line for now. After that, you should be ready to use the hand files.
Step 4: Shaping the Body
Now is where the fun really begins. It's time to begin the shaping of the actual body to look like a lizard.
- Using hand files begin to smooth out the corners and round everything out. You can see I marked with a pen the areas where I want to highlight and not file down too much. Think about it as a topographical map. Circle the high spots so you know to work away from that area when filing things down. This is where looking at lizard anatomy can really help. Look online for 3D images of lizards. There are many to choose from. Find one that works best for you. This can greatly help you visualize where/how to shape your lizard.
- Use your hand files and get busy. For the areas that need a lot of material to be removed if you're comfortable with a flap wheel on your grinder or Dremel, use them If you'd like. Just be very cautious. I found doing it with a hand file allows for much more accurate work. File, check your reference. File more, check your reference again. Keep filing until you are satisfied completely with the shape that you've created. Once you are at that point use a buffing pad on your grinder or Dremel as well as fine grit, Emery cloth and get it smooth as can be, the smoother the better.
- Once satisfied with the shape, place it on top of a copy of your reference image. Mark where the eyes, legs and arms should attach to the body. I put a line in the direction that the arms and legs go so that way I can drill the holes appropriately in the same direction. Mark that location with pen and then drill the holes with the appropriate size drill bit on the sides of the lizard. In this case it was a 3/16" bit. Don't forget to use a center punch before drilling if you have one available. The eyes can be any size or location on the head that you'd prefer. You'll have a chance to slightly adjust those at any point prior to the heat treatment at the very end. Just use your reference material and pick the spot and drill accordingly.
- After your holes are drilled, you can place your lizard body back on top of the reference image. Layout the arms into position to double check your hole locations. If everything lines up, continue to clean and polish the body as much as you can.
Step 5: Creating the Tail
Up to this point your tail has been nothing but a straight block of metal. This is where you get to make it look really cool and its completely optional if you'd like to do it this way.
- Using a grinder with a flap wheel (or Dremel or hand files) shape your tail into a point. feel free to draw points on the side if you'd like, but ultimately try to evenly work the material down to an "ice pick"-like form with 4 flat sides, and slightly rounded corners. Round the tip of the tail off so its not too pointy or sharp.
- Once you've done that use your propane torch and heat the tail. Begin at the base (or toward the base) of the tail until it's red hot. You are about to do something known in blacksmithing called a "reverse twist" (look online for further info on this technique if this step is unclear) ... Once the material is glowing red hot, use pliers to twist the material. Try to go slow and keep your material hot working the heat from the base of the tail towards the tip as you twist. Once you've done one full 360 degree twist, stop and twist the other direction as you're working the heat down towards the tip. Continue to do this process until you reach the end of the tail. Be careful not to twist too tightly or your tail may break off, so take your time!
- Once you've completed twisting, continue to heat the tail and shape it into position. The thickness of the tail, amount of curve it has, and in what direction the tail lays is completely your choice.
- When it looks good and it's in the right position, let it cool. After it has cooled down take some fine grit sandpaper, and sand down the very edges of the twists just a little bit, removing a little of the darkened material the heat created. That sanding will create a lighter, and cool contrast that showcase the lines on the edges of your twists, really bringing out the highlights and definition of what you have just done
Step 6: Attaching the Arms and Legs to the Body
Attaching the arms and legs is pretty simple. Hopefully you made your holes on the body large enough to accommodate the ends of your arms and legs to be inserted into the hole. You may need to make some adjustments by either widening the holes on the body, or sanding down the ends of your limbs a little more, but it just needs to be enough to hold the limb in position until you weld it. Once you place the arms and legs into position and everything looks good, weld both arms and both legs. Once all of the limbs are welded, you may need to use the torch to heat them up a little bit ad adjust the limbs so that everything lays flat and flush to the ground. Touch up your welds with fine grit sandpaper or emery cloth if needed.
In this step, I use a TIG welder, but you can accomplish the same results using solder. Simply add flux to the holes on the body, roll a small piece of solder and place inside the holes, place all arms and legs into position, and heat with a torch until the solder melts. Let it cool and you are done. Once soldered, you would not be able to heat treat, and do step seven UNLESS, you decide to do it at the same time. In that case, you'll have to combine steps 6 and 7 to do simultaneously.
Step 7: Using Heat to Color the Lizard
Prep your lizard well by getting it absolutely as smooth as possible everywhere. This will be the final opportunity to do so. Make sure to remove all oils from the material. Then heat until you've reached your desired color.
- Put on some rubber gloves
- Pour some acetone or alcohol into a rag or paper towel and wipe down the entire lizard throughly.
- Let the material dry and place in an area where the heat can move freely. Scrap 2" square tubing works great for this
- Remove the moisture from the metal. Metal can hold moisture. Remove it by slightly heating the metal and then letting it cool. The metal will literally look like it has been steamed when the moisture is being removed. Now you're ready to begin the heat treatment
- You can change the color of steel by heating it within certain temperature ranges. The purples and blues I was aiming for take effect from 520° to 620°F
- Use your propane, torch, and slowly begin to heat the lizard, focusing on the thickest parts in the center first but evenly moving the heat around. The thinnest parts will change color of the fastest. If you heat it too much and go past the desired color range you're looking for, you can't go backwards. You would have to sand it down and start over, so take your time and keep heating until you've reached the desired effect.
- Heat treating is like driving a boat. You need to lay off the gas prior to where you want to stop. The residual heat will not stop immediately, so I advise to be cautious and pull the heat away just before you're at the desired amount of color.
- Let the metal cool naturally and slowly.
- Once it is at room temperature spray a clear coat of your choice to protect the finish. I personally prefer a high gloss look for this type of project
Step 8: Final Step: Adding the Eyes
Your lizard is almost done! At this point you should be proud of yourself and how great it looks! This is perhaps the simplest step, but if you make a mistake, it can have devastating results. (I found that out the hard way). Hopefully throughout this project, you have something in mind you would like to use for the eyes. If not, no problem! It literally can be ANYTHING you want that fits within the holes you previously drilled. For this project, I bought a package of flat back rounded pearl gems of various sizes. The hard part is deciding on a color, but these were 6 mm in size. Choose a super glue or any quick drying glue that you like, and glue them in. Go light with the glue though because it's very difficult to wipe any excess glue off and not disturb the beautiful color and clear coat. I suggest squirting a little glue onto a paper plate, and using a toothpick and dab a little in the hole for the eye location, then place your gem on top of it. let it dry and....... YOU ARE DONE!
It's amazing what beautiful things can be created from some simple scrap material.
I'd love to hear your feedback!
Let me know what you liked, or didn't like about this tutorial. If you do the project, let me know how it turns out. And, If you'd like to see anything more or reach me directly you can find me on my YouTube channel that is in the videos of this instruction.
Thanks for checking it out!
-CMH Metalwork
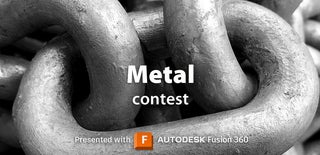
Grand Prize in the
Metal Contest